PETRONAS LUBRICANTS ITALY s.p.a., VILLASTELLONE (TO):
BIERRE AUTOMAZIONI PERFORMS THE RE-POSITIONING AND THE ELECTRIC / MECHANICAL REVAMPING OF 2 “LITA” DEPALLETISERS.
The Customer
Petronas is a Malaysian multinational company operating in the oil market. Established in 1974, it is currently present in more than 65 countries worldwide and works with the world’s major oil companies. At its facility in Villastellone (TO), Petronas Lubricants Italy s.p.a.’s main activities concern the production of lubricating oils and engine additives.
The need
The packaging department had 2 old depalletisers for metal buckets marked LITA, which respectively support 2 linear volumetric fillers. The machinery in question was in working order, but practically unused due to the fact the only format it can handle is no longer used. They required maintenance; they were equipped with an obsolete electrical panel, the safety devices were not in line with current standards and their location within the facility no longer met the logistical needs of the customer, which have changed over the years to achieve greater levels of safety for Petronas operators. The reduction in facility downtimes and the budget did not allow the machines to be replaced with new ones, however it was particularly important to have the CE marking for both machines, for obvious reasons regarding worker safety.
Customer requirements:
– CE marking for both machines.
– Mechanical adjustment to the new depalletising format in 20lt plastic cans, and removal of the equipment that permitted the used of the “metal bucket” format.
– A slight increase in hourly production capacity.
– General machine maintenance to restore it “like new”.
Bierre Automazioni was entrusted with the task of shutting down the filling lines during the Christmas holidays.
The solution chosen
The machines were then disassembled and transported to our workshop for all the necessary maintenance work, format conversion and CE re-certification.The “new” LITA depalletisers then underwent the following:
– The fitting of a new electrical panel and new perimeter safety guards with dedicated safety circuit
– The fitting of new electrical system, complete with FTC, sensors and certified safety barriers.
– Complete repainting
– Mechanical modifications for the new format
– General mechanical maintenance
– Complete testing with the new electrical panel and new machine configuration.
– CE certification, complete with new plate and new use & maintenance manual as required by lawThe machines were then re-positioned in other areas of the facility in order to satisfy Petronas’ requirements.
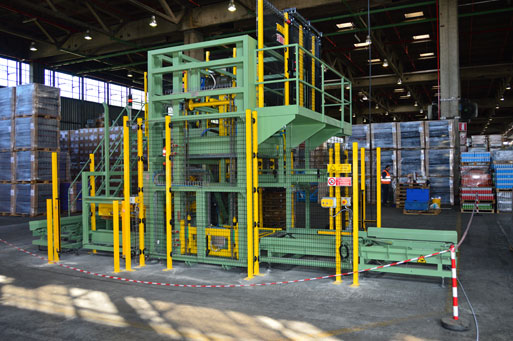
RESULTS ACHIEVED
“”The complete revamping of the old depalletisers has allowed Petronas to utilise, once again, the two machine that otherwise would have been dismantled, and the work carried out has also resulted in significant economic savings compared to the purchase of two new machines. The increase in productivity has made it possible to support all the production of the servo filling lines, but the costs involved and system downtimes were much lower than a new installation.””
Petronas Lubricants Italy s.p.a., Villastellone (to)
Contact:
Fabrizio Maestri
Sales Manager / Senior Engineer
(f.maestri@bierreautomazioni.com)